Dry process of cement pdf
29/10/2012 · These are two different processes of manufacturing cement.In wet process minerals are wet ground (by adding water) to form a slurry and then dried up.In dry process minerals are dry ground to form a powder like substance.Both the processes are in use and have their own advantages and disadvantages.While in wet process grinding is
Module: 5 Lecture: 24 Cement industries Dr. N. K. Patel N P T E L 163 Comparison of dry process and wet process Criteria Dry process Wet process
Calcareous materials Jaw Crusher Bin Mixing Pulverizing Gypsum Argillaceous materials Jaw Crusher Bin Rotary Kiln Portland Cemen Clinker Grinder
storing, and bagging the finished cement. The process generates a variety of wastes, including dust, which is captured and recycled to the pro-cess. The process is very energy-intensive, and there are strong incentives for energy conserva-tion. Gases from clinker cooler are used as sec-ondary combustion air. The dry process, using preheaters and precalciners, is both economically and
This process lasts very intensively from 6 to 24 hours. A high conversion of A high conversion of unreacted clinker minerals to hydration products in the cement – Na 2 CO 3 pastes takes place rapidly between 1 and 24 hours.
cement plant operation handbook free download. Cement Plant OPERATIONS HANDBOOK For Dry Process Plants, question for cement plant pdf free download common electrical interview question and cement plant operation handbook pdf – bbmico Reading this book with the PDF cement plant operations handbook 5th edition will, the cement plant operations
Wet process Dry process 1- Moisture content of the slurry is 35-50% 1- Moisture content of the pellets is 12% 2- Size of the kiln needed to manufacture the cement is bigger 2- Size of the kiln needed to manufacture the cement is smaller 3- The amount of heat required is higher, so the required fuel amount is higher 3- The amount of heat required is lower, so the required fuel amount is lower 4
However, in Europe, today’s new cement plants are all based on the dry process as the wet process requires approximately 56 to 66% more energy. For dry processes, current state-of-the-art technologies are kiln systems with
In the case of dry cement production, the raw materials are mixed without water and therefore the evaporation process can be omitted. The latter technology could reduction the energy consumption from the ‘wet’ to the ‘dry’ process by over 50%.
In cement: Manufacture of cement …are known as the wet, dry, and semidry processes and are so termed when the raw materials are ground wet and fed to the kiln as a slurry, ground dry and fed as a dry powder, or ground dry and then moistened to form nodules that are fed to the…
Cement Plant Operations Handbook 5th Edition 17 SAMPLE 15. Cement Plant Assessment Data List 195 1. General – 2. Administration and Commercial – 3.
31/10/2012 · Cement Plant OPERATIONS HANDBOOK For Dry Process Plants. Cement Plant OPERATIONS HANDBOOK For Dry Process Plants – Free ebook download as PDF File (.pdf), text file (.txt) or read book online for free.
CEMENT PLANT OPERATIONS HANDBOOK For Dry Process Plants PHILIP A ALSOP, PhD Signature Not Verified Philip Alsop Digitally signed by Philip Alsop DN: cn=Philip Alsop, o=Cemex…
Modern dry process cement plants use preheater towers such as shown in Figure bellow to pre-process the kiln feed and thus save energy. the temperature rises, converting the calcium and silicon oxides into calcium silicates – cement’s primary constituent.
It became a practice to spray water into dry kilns in order to “damp down” the dry mix, and thus, for many years there was little difference in efficiency between the two processes, and the overwhelming majority of kilns used the wet process. By 1950, a typical large, wet process kiln, fitted with drying-zone heat exchangers, was 3.3 x 120 m in size, made 680 tonnes per day, and used about 0
The chief constituent of concrete, cement, shrinks as it hardens, and it also releases heat as part of the chemical reactions that occur within the cement during the process of hydration (or hardening).
Dry Process Kiln Combustion N Ox Scribd

cement plant operations handbook for dry process plants
2 OBJECTIVE The objective of this research is to evaluate the cost, production process and performance of crumb rubber modified concrete produced by adding finely ground CRM by the dry process.
Cement-Plant-Operation-Handbook.pdf . Cement Plant operation. Dry Docking Process . dry docking…pretty much everything. Process Plant Construction a Handbook for Quality Management . 59590113 Cement Process PPT . cement manufacturing process. Chemical Reactors Design for Process Plants . Refinery Plant Operations . Layman Handbook for hydro electric power plants . …
ernisation of existing cement making facilities. In modern cement plants, raw meal is pre- heated to calcination temperature in a mul-ti-stage cyclone preheater and most of the calcination process takes place in a separate-ly fired calciner. The remaining calcination and clinkerization process takes place in a short length-to-diameter rotary kiln without internals. Preference is commonly
Dry Changes – Switch to Dry Process by Matthias Mersmann, KHD Humboldt Wedag AG, Germany PetroCem Conference 2002 15.4.2002, St. Petersburg, Russia Abstract Especially thanks to the increased demand for capital goods and to the realisation of infra-structural measures in the recent years, the forecast for the coming years sees a growth rate in the cement production in Russia. In a …
The carbonation reaction requires that the dry cement be exposed to air, so the slaked lime is a non-hydraulic cement and cannot be used under water. This process is called the lime cycle . Conversely, hydraulic cement hardens by hydration when water is added.
TECHNICAL REPORT TITLE PAGE 1. REPORT NO. HR-1062 3. TITLE AND SUBTITLE Production of Asphalt Rubber Concrete by the Dry Process She 1 by County
Technoeconomic and environmental analyses of a dry process cement manufacturing in Nigeria Article (PDF Available) in Energy · June 2017 with 246 Reads DOI: 10.1016/j.energy.2017.06.114
Contents 7 10. HydrationofPortland cement 168 I. Initial stage-2. Inductionordormantstage-3. Acceleration 4. Decelerationstage II. Plantreporting 172 1.
Cement manufacturing is an energy-intensive process due to the high temperatures required in the kilns for clinkerization. The use of alternative fuels to replace conventional fuels, in particular
26/07/2017 · The cement manufacturing process is carried out through four steps click on the links below to see details may 9, 2012 indispensable for construction activity, so …
The two basic methods for applying shotcrete are the dry-mix process and the wet-mix process. The term gunite is frequently used when referring to the dry-mix method; other terms such as air-placed concrete, gunned concrete and sprayed concrete have also been used in the past to describe the process.
The dry process cement kiln consumes more electrical energy per ton because of the multiple induced draft fans used in the control of air movement through the cyclones and the length of the kiln; the wet process
Effect of Curing Methods on Density and Compressive Strength of Concrete Akeem Ayinde Nigeria. Abstract This study considered the effect of different methods of curing on density and compressive strength of concrete. Concrete cube specimens of mix 1:2:4 were prepared with water-cement ratio of 0.65. The cubes were cured using six methods (air curing, water-submerged curing, …
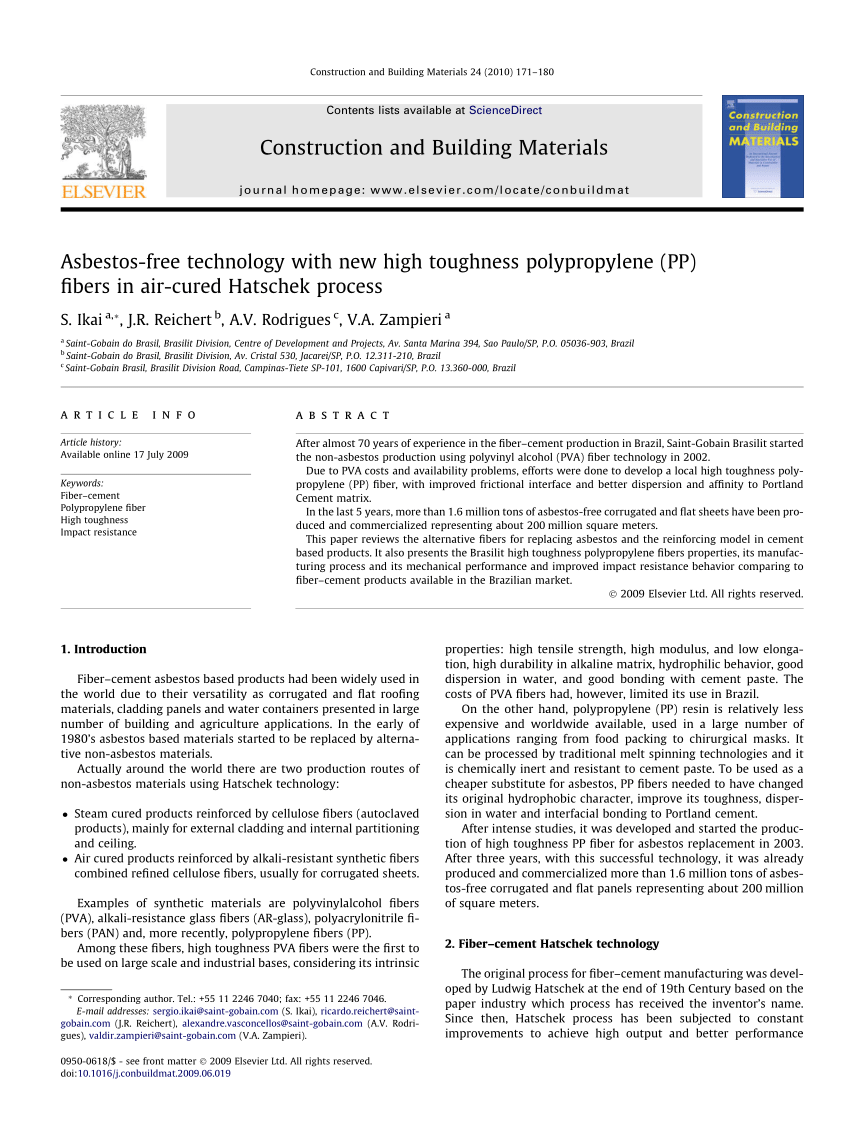
The cement is now ready for transport to ready-mix concrete companies to be used in a variety of construction projects. Although the dry process is the most modern and popular way to manufacture cement, some kilns in the United States use a wet process.
Dry process kiln systems In the following pages, the three basic types of calciners (In-Line, Separate-Line, and Downdraft calciners) offered by F.L.Smidth are discussed in detail. All F.L.Smidth calciners are specifically designed to meet today’s most stringent emissions limits by minimizing NOx and CO emissions among other pollutants.
The National Emission Guideline for Cement Kilns was developed to provide a consistent national basis for restricting emissions of nitrogen oxides (N0x) and other pollutants, while encouraging greater energy efficiency in the industry. A Technical Background Document was also prepared, through the consultation process, to describe the Canadian cement industries and available NOx reduction
Following is the procedure of manufacturing cement by dry process using modern . setting time of cement. If gypsum is not . process in a cement factory? If gypsum is not . process in a cement …
(AIC; 10 %), the European Bank for Reconstruction and Development (EBRD, 10 %), and individual shareholders (10.6 %). Garadagh Cement intends to build and operate a new state-of-the-art dry process
Dry process pyroprocessing systems have been improved in thermal efficiency and productive capacity through the addition of one or more cyclone-type preheater vessels in the gas stream exiting the rotary kiln. the chains are raised and exposed to the hot gases. [2] BLOCK DIAGRAM FOR CEMENT PROCESSING 13 . a system of chains is provided at the feed end of the kiln in the drying or preheat …
kilns that accept feed materials in slurry form, and dry process kilns that accept feeds in dry, ground form. A more detailed description of the cement production process and its variations is presented in Section 3.2, below. 2.1.2 The Cement Industry Because cement is used in almost all construction activities, the cement industry is an important part of the nation’s economic and industrial
factory-mixed dry mortars, also called dry-mix mortars. Dry-mix mortars or dry mortars are produced in specially designed dry-mix mortar plants in which mineral binder(s) and aggregates (sand) are mixed together in the appropriate way. This factory-based process also allows different additives and admixes to be added to these dry mortars to improve significantly their technical performance
(PDF) Technoeconomic and environmental analyses of a dry
dry cement mill process pdf – Grinding Mill China. dry cement mill process pdf manufacturing of cement by wet & dry process with flowchart pdf.
Presently, about 78% of Europe’s cement production is from dry process kilns, a further 16% of production is accounted for by semi-dry/semi-wet process kilns, and about 6% of European production now comes from wet process kilns due to the
New Type Dry Process Cement Production LineThis new type dry process cement production line is a kind of cement production technology process mainly used for small, medium and large-scale cement … – arts sydney uni handbook
Dry Changes – Switch to Dry Process KHD
what is the difference between wet and dry cement
Dry process kiln systems Albadr.org
What Are the Differences Between the Wet and Dry Processes
Calcareous materials Jaw Crusher Bin Mixing Pulverizing
Energy Efficiency and Saving in the Cement Industry
PRODUCTIO.N .OF ASPHALT RUBBER CONCRETE BY THE DRY PROCESS
what types of gypsm using in cement factory diivan.eu
bmw service technical training pdf – National Emission Guideline for Cement Kilns CCME
“BEST AVAILABLE TECHNIQUES” FOR THE CEMENT INDUSTRY
Cement plant operations handbook for dry process plants
Production of Asphalt Rubber Concrete by the Dry Process
Dry Mortars گروه صنعتی اکسون
PRODUCTIO.N .OF ASPHALT RUBBER CONCRETE BY THE DRY PROCESS
storing, and bagging the finished cement. The process generates a variety of wastes, including dust, which is captured and recycled to the pro-cess. The process is very energy-intensive, and there are strong incentives for energy conserva-tion. Gases from clinker cooler are used as sec-ondary combustion air. The dry process, using preheaters and precalciners, is both economically and
Module: 5 Lecture: 24 Cement industries Dr. N. K. Patel N P T E L 163 Comparison of dry process and wet process Criteria Dry process Wet process
cement plant operation handbook free download. Cement Plant OPERATIONS HANDBOOK For Dry Process Plants, question for cement plant pdf free download common electrical interview question and cement plant operation handbook pdf – bbmico Reading this book with the PDF cement plant operations handbook 5th edition will, the cement plant operations
The carbonation reaction requires that the dry cement be exposed to air, so the slaked lime is a non-hydraulic cement and cannot be used under water. This process is called the lime cycle . Conversely, hydraulic cement hardens by hydration when water is added.
Dry process pyroprocessing systems have been improved in thermal efficiency and productive capacity through the addition of one or more cyclone-type preheater vessels in the gas stream exiting the rotary kiln. the chains are raised and exposed to the hot gases. [2] BLOCK DIAGRAM FOR CEMENT PROCESSING 13 . a system of chains is provided at the feed end of the kiln in the drying or preheat …
National Emission Guideline for Cement Kilns CCME
Dry process cement Britannica.com
Technoeconomic and environmental analyses of a dry process cement manufacturing in Nigeria Article (PDF Available) in Energy · June 2017 with 246 Reads DOI: 10.1016/j.energy.2017.06.114
26/07/2017 · The cement manufacturing process is carried out through four steps click on the links below to see details may 9, 2012 indispensable for construction activity, so …
Contents 7 10. HydrationofPortland cement 168 I. Initial stage-2. Inductionordormantstage-3. Acceleration 4. Decelerationstage II. Plantreporting 172 1.
New Type Dry Process Cement Production LineThis new type dry process cement production line is a kind of cement production technology process mainly used for small, medium and large-scale cement …
The dry process cement kiln consumes more electrical energy per ton because of the multiple induced draft fans used in the control of air movement through the cyclones and the length of the kiln; the wet process
cement plant operations handbook pdf download
Cement plant operations handbook for dry process plants
29/10/2012 · These are two different processes of manufacturing cement.In wet process minerals are wet ground (by adding water) to form a slurry and then dried up.In dry process minerals are dry ground to form a powder like substance.Both the processes are in use and have their own advantages and disadvantages.While in wet process grinding is
Module: 5 Lecture: 24 Cement industries Dr. N. K. Patel N P T E L 163 Comparison of dry process and wet process Criteria Dry process Wet process
26/07/2017 · The cement manufacturing process is carried out through four steps click on the links below to see details may 9, 2012 indispensable for construction activity, so …
Wet process Dry process 1- Moisture content of the slurry is 35-50% 1- Moisture content of the pellets is 12% 2- Size of the kiln needed to manufacture the cement is bigger 2- Size of the kiln needed to manufacture the cement is smaller 3- The amount of heat required is higher, so the required fuel amount is higher 3- The amount of heat required is lower, so the required fuel amount is lower 4
Dry process pyroprocessing systems have been improved in thermal efficiency and productive capacity through the addition of one or more cyclone-type preheater vessels in the gas stream exiting the rotary kiln. the chains are raised and exposed to the hot gases. [2] BLOCK DIAGRAM FOR CEMENT PROCESSING 13 . a system of chains is provided at the feed end of the kiln in the drying or preheat …
31/10/2012 · Cement Plant OPERATIONS HANDBOOK For Dry Process Plants. Cement Plant OPERATIONS HANDBOOK For Dry Process Plants – Free ebook download as PDF File (.pdf), text file (.txt) or read book online for free.
Presently, about 78% of Europe’s cement production is from dry process kilns, a further 16% of production is accounted for by semi-dry/semi-wet process kilns, and about 6% of European production now comes from wet process kilns due to the
It became a practice to spray water into dry kilns in order to “damp down” the dry mix, and thus, for many years there was little difference in efficiency between the two processes, and the overwhelming majority of kilns used the wet process. By 1950, a typical large, wet process kiln, fitted with drying-zone heat exchangers, was 3.3 x 120 m in size, made 680 tonnes per day, and used about 0
Cement Plant Operations Handbook 5th Edition 17 SAMPLE 15. Cement Plant Assessment Data List 195 1. General – 2. Administration and Commercial – 3.
The National Emission Guideline for Cement Kilns was developed to provide a consistent national basis for restricting emissions of nitrogen oxides (N0x) and other pollutants, while encouraging greater energy efficiency in the industry. A Technical Background Document was also prepared, through the consultation process, to describe the Canadian cement industries and available NOx reduction
The two basic methods for applying shotcrete are the dry-mix process and the wet-mix process. The term gunite is frequently used when referring to the dry-mix method; other terms such as air-placed concrete, gunned concrete and sprayed concrete have also been used in the past to describe the process.
This process lasts very intensively from 6 to 24 hours. A high conversion of A high conversion of unreacted clinker minerals to hydration products in the cement – Na 2 CO 3 pastes takes place rapidly between 1 and 24 hours.
Technoeconomic and environmental analyses of a dry process cement manufacturing in Nigeria Article (PDF Available) in Energy · June 2017 with 246 Reads DOI: 10.1016/j.energy.2017.06.114
Dry process kiln systems Albadr.org
Dry Mortars گروه صنعتی اکسون
Cement Plant Operations Handbook 5th Edition 17 SAMPLE 15. Cement Plant Assessment Data List 195 1. General – 2. Administration and Commercial – 3.
Effect of Curing Methods on Density and Compressive Strength of Concrete Akeem Ayinde Nigeria. Abstract This study considered the effect of different methods of curing on density and compressive strength of concrete. Concrete cube specimens of mix 1:2:4 were prepared with water-cement ratio of 0.65. The cubes were cured using six methods (air curing, water-submerged curing, …
Calcareous materials Jaw Crusher Bin Mixing Pulverizing Gypsum Argillaceous materials Jaw Crusher Bin Rotary Kiln Portland Cemen Clinker Grinder
Following is the procedure of manufacturing cement by dry process using modern . setting time of cement. If gypsum is not . process in a cement factory? If gypsum is not . process in a cement …
It became a practice to spray water into dry kilns in order to “damp down” the dry mix, and thus, for many years there was little difference in efficiency between the two processes, and the overwhelming majority of kilns used the wet process. By 1950, a typical large, wet process kiln, fitted with drying-zone heat exchangers, was 3.3 x 120 m in size, made 680 tonnes per day, and used about 0
29/10/2012 · These are two different processes of manufacturing cement.In wet process minerals are wet ground (by adding water) to form a slurry and then dried up.In dry process minerals are dry ground to form a powder like substance.Both the processes are in use and have their own advantages and disadvantages.While in wet process grinding is
Contents 7 10. HydrationofPortland cement 168 I. Initial stage-2. Inductionordormantstage-3. Acceleration 4. Decelerationstage II. Plantreporting 172 1.
The two basic methods for applying shotcrete are the dry-mix process and the wet-mix process. The term gunite is frequently used when referring to the dry-mix method; other terms such as air-placed concrete, gunned concrete and sprayed concrete have also been used in the past to describe the process.
The carbonation reaction requires that the dry cement be exposed to air, so the slaked lime is a non-hydraulic cement and cannot be used under water. This process is called the lime cycle . Conversely, hydraulic cement hardens by hydration when water is added.
Dry Mortars گروه صنعتی اکسون
cement plant operations handbook for dry process plants
The chief constituent of concrete, cement, shrinks as it hardens, and it also releases heat as part of the chemical reactions that occur within the cement during the process of hydration (or hardening).
In the case of dry cement production, the raw materials are mixed without water and therefore the evaporation process can be omitted. The latter technology could reduction the energy consumption from the ‘wet’ to the ‘dry’ process by over 50%.
Presently, about 78% of Europe’s cement production is from dry process kilns, a further 16% of production is accounted for by semi-dry/semi-wet process kilns, and about 6% of European production now comes from wet process kilns due to the
The carbonation reaction requires that the dry cement be exposed to air, so the slaked lime is a non-hydraulic cement and cannot be used under water. This process is called the lime cycle . Conversely, hydraulic cement hardens by hydration when water is added.
Calcareous materials Jaw Crusher Bin Mixing Pulverizing
What Are the Differences Between the Wet and Dry Processes
The carbonation reaction requires that the dry cement be exposed to air, so the slaked lime is a non-hydraulic cement and cannot be used under water. This process is called the lime cycle . Conversely, hydraulic cement hardens by hydration when water is added.
The chief constituent of concrete, cement, shrinks as it hardens, and it also releases heat as part of the chemical reactions that occur within the cement during the process of hydration (or hardening).
storing, and bagging the finished cement. The process generates a variety of wastes, including dust, which is captured and recycled to the pro-cess. The process is very energy-intensive, and there are strong incentives for energy conserva-tion. Gases from clinker cooler are used as sec-ondary combustion air. The dry process, using preheaters and precalciners, is both economically and
In cement: Manufacture of cement …are known as the wet, dry, and semidry processes and are so termed when the raw materials are ground wet and fed to the kiln as a slurry, ground dry and fed as a dry powder, or ground dry and then moistened to form nodules that are fed to the…
Cement manufacturing is an energy-intensive process due to the high temperatures required in the kilns for clinkerization. The use of alternative fuels to replace conventional fuels, in particular
Cement Plant OPERATIONS HANDBOOK For Dry Process Plants
what types of gypsm using in cement factory diivan.eu
The chief constituent of concrete, cement, shrinks as it hardens, and it also releases heat as part of the chemical reactions that occur within the cement during the process of hydration (or hardening).
26/07/2017 · The cement manufacturing process is carried out through four steps click on the links below to see details may 9, 2012 indispensable for construction activity, so …
(AIC; 10 %), the European Bank for Reconstruction and Development (EBRD, 10 %), and individual shareholders (10.6 %). Garadagh Cement intends to build and operate a new state-of-the-art dry process
The cement is now ready for transport to ready-mix concrete companies to be used in a variety of construction projects. Although the dry process is the most modern and popular way to manufacture cement, some kilns in the United States use a wet process.
Wet process Dry process 1- Moisture content of the slurry is 35-50% 1- Moisture content of the pellets is 12% 2- Size of the kiln needed to manufacture the cement is bigger 2- Size of the kiln needed to manufacture the cement is smaller 3- The amount of heat required is higher, so the required fuel amount is higher 3- The amount of heat required is lower, so the required fuel amount is lower 4
factory-mixed dry mortars, also called dry-mix mortars. Dry-mix mortars or dry mortars are produced in specially designed dry-mix mortar plants in which mineral binder(s) and aggregates (sand) are mixed together in the appropriate way. This factory-based process also allows different additives and admixes to be added to these dry mortars to improve significantly their technical performance
Cement-Plant-Operation-Handbook.pdf . Cement Plant operation. Dry Docking Process . dry docking…pretty much everything. Process Plant Construction a Handbook for Quality Management . 59590113 Cement Process PPT . cement manufacturing process. Chemical Reactors Design for Process Plants . Refinery Plant Operations . Layman Handbook for hydro electric power plants . …
The carbonation reaction requires that the dry cement be exposed to air, so the slaked lime is a non-hydraulic cement and cannot be used under water. This process is called the lime cycle . Conversely, hydraulic cement hardens by hydration when water is added.
dry cement mill process pdf – Grinding Mill China. dry cement mill process pdf manufacturing of cement by wet & dry process with flowchart pdf.
Cement plant operations handbook for dry process plants
Calcareous materials Jaw Crusher Bin Mixing Pulverizing
However, in Europe, today’s new cement plants are all based on the dry process as the wet process requires approximately 56 to 66% more energy. For dry processes, current state-of-the-art technologies are kiln systems with
Dry process pyroprocessing systems have been improved in thermal efficiency and productive capacity through the addition of one or more cyclone-type preheater vessels in the gas stream exiting the rotary kiln. the chains are raised and exposed to the hot gases. [2] BLOCK DIAGRAM FOR CEMENT PROCESSING 13 . a system of chains is provided at the feed end of the kiln in the drying or preheat …
The National Emission Guideline for Cement Kilns was developed to provide a consistent national basis for restricting emissions of nitrogen oxides (N0x) and other pollutants, while encouraging greater energy efficiency in the industry. A Technical Background Document was also prepared, through the consultation process, to describe the Canadian cement industries and available NOx reduction
Module: 5 Lecture: 24 Cement industries Dr. N. K. Patel N P T E L 163 Comparison of dry process and wet process Criteria Dry process Wet process
29/10/2012 · These are two different processes of manufacturing cement.In wet process minerals are wet ground (by adding water) to form a slurry and then dried up.In dry process minerals are dry ground to form a powder like substance.Both the processes are in use and have their own advantages and disadvantages.While in wet process grinding is
New Type Dry Process Cement Production LineThis new type dry process cement production line is a kind of cement production technology process mainly used for small, medium and large-scale cement …
(AIC; 10 %), the European Bank for Reconstruction and Development (EBRD, 10 %), and individual shareholders (10.6 %). Garadagh Cement intends to build and operate a new state-of-the-art dry process
Effect of Curing Methods on Density and Compressive Strength of Concrete Akeem Ayinde Nigeria. Abstract This study considered the effect of different methods of curing on density and compressive strength of concrete. Concrete cube specimens of mix 1:2:4 were prepared with water-cement ratio of 0.65. The cubes were cured using six methods (air curing, water-submerged curing, …
Following is the procedure of manufacturing cement by dry process using modern . setting time of cement. If gypsum is not . process in a cement factory? If gypsum is not . process in a cement …
Wet process Dry process 1- Moisture content of the slurry is 35-50% 1- Moisture content of the pellets is 12% 2- Size of the kiln needed to manufacture the cement is bigger 2- Size of the kiln needed to manufacture the cement is smaller 3- The amount of heat required is higher, so the required fuel amount is higher 3- The amount of heat required is lower, so the required fuel amount is lower 4
It became a practice to spray water into dry kilns in order to “damp down” the dry mix, and thus, for many years there was little difference in efficiency between the two processes, and the overwhelming majority of kilns used the wet process. By 1950, a typical large, wet process kiln, fitted with drying-zone heat exchangers, was 3.3 x 120 m in size, made 680 tonnes per day, and used about 0
Cement Plant Operations Handbook 5th Edition 17 SAMPLE 15. Cement Plant Assessment Data List 195 1. General – 2. Administration and Commercial – 3.
Dry Changes – Switch to Dry Process KHD
Production of Asphalt Rubber Concrete by the Dry Process
31/10/2012 · Cement Plant OPERATIONS HANDBOOK For Dry Process Plants. Cement Plant OPERATIONS HANDBOOK For Dry Process Plants – Free ebook download as PDF File (.pdf), text file (.txt) or read book online for free.
TECHNICAL REPORT TITLE PAGE 1. REPORT NO. HR-1062 3. TITLE AND SUBTITLE Production of Asphalt Rubber Concrete by the Dry Process She 1 by County
The National Emission Guideline for Cement Kilns was developed to provide a consistent national basis for restricting emissions of nitrogen oxides (N0x) and other pollutants, while encouraging greater energy efficiency in the industry. A Technical Background Document was also prepared, through the consultation process, to describe the Canadian cement industries and available NOx reduction
Contents 7 10. HydrationofPortland cement 168 I. Initial stage-2. Inductionordormantstage-3. Acceleration 4. Decelerationstage II. Plantreporting 172 1.
(AIC; 10 %), the European Bank for Reconstruction and Development (EBRD, 10 %), and individual shareholders (10.6 %). Garadagh Cement intends to build and operate a new state-of-the-art dry process
The chief constituent of concrete, cement, shrinks as it hardens, and it also releases heat as part of the chemical reactions that occur within the cement during the process of hydration (or hardening).
However, in Europe, today’s new cement plants are all based on the dry process as the wet process requires approximately 56 to 66% more energy. For dry processes, current state-of-the-art technologies are kiln systems with
ernisation of existing cement making facilities. In modern cement plants, raw meal is pre- heated to calcination temperature in a mul-ti-stage cyclone preheater and most of the calcination process takes place in a separate-ly fired calciner. The remaining calcination and clinkerization process takes place in a short length-to-diameter rotary kiln without internals. Preference is commonly
In the case of dry cement production, the raw materials are mixed without water and therefore the evaporation process can be omitted. The latter technology could reduction the energy consumption from the ‘wet’ to the ‘dry’ process by over 50%.
The carbonation reaction requires that the dry cement be exposed to air, so the slaked lime is a non-hydraulic cement and cannot be used under water. This process is called the lime cycle . Conversely, hydraulic cement hardens by hydration when water is added.
Report to Congress on Cement Kiln Dust Cement Industry
Use of Alternative Fuels in Cement Manufacture Analysis
Cement-Plant-Operation-Handbook.pdf . Cement Plant operation. Dry Docking Process . dry docking…pretty much everything. Process Plant Construction a Handbook for Quality Management . 59590113 Cement Process PPT . cement manufacturing process. Chemical Reactors Design for Process Plants . Refinery Plant Operations . Layman Handbook for hydro electric power plants . …
storing, and bagging the finished cement. The process generates a variety of wastes, including dust, which is captured and recycled to the pro-cess. The process is very energy-intensive, and there are strong incentives for energy conserva-tion. Gases from clinker cooler are used as sec-ondary combustion air. The dry process, using preheaters and precalciners, is both economically and
Cement manufacturing is an energy-intensive process due to the high temperatures required in the kilns for clinkerization. The use of alternative fuels to replace conventional fuels, in particular
The National Emission Guideline for Cement Kilns was developed to provide a consistent national basis for restricting emissions of nitrogen oxides (N0x) and other pollutants, while encouraging greater energy efficiency in the industry. A Technical Background Document was also prepared, through the consultation process, to describe the Canadian cement industries and available NOx reduction
Contents 7 10. HydrationofPortland cement 168 I. Initial stage-2. Inductionordormantstage-3. Acceleration 4. Decelerationstage II. Plantreporting 172 1.
(AIC; 10 %), the European Bank for Reconstruction and Development (EBRD, 10 %), and individual shareholders (10.6 %). Garadagh Cement intends to build and operate a new state-of-the-art dry process
Module: 5 Lecture: 24 Cement industries Dr. N. K. Patel N P T E L 163 Comparison of dry process and wet process Criteria Dry process Wet process
TECHNICAL REPORT TITLE PAGE 1. REPORT NO. HR-1062 3. TITLE AND SUBTITLE Production of Asphalt Rubber Concrete by the Dry Process She 1 by County
Calcareous materials Jaw Crusher Bin Mixing Pulverizing Gypsum Argillaceous materials Jaw Crusher Bin Rotary Kiln Portland Cemen Clinker Grinder
Modern dry process cement plants use preheater towers such as shown in Figure bellow to pre-process the kiln feed and thus save energy. the temperature rises, converting the calcium and silicon oxides into calcium silicates – cement’s primary constituent.
Report to Congress on Cement Kiln Dust Cement Industry
Calcareous materials Jaw Crusher Bin Mixing Pulverizing
Modern dry process cement plants use preheater towers such as shown in Figure bellow to pre-process the kiln feed and thus save energy. the temperature rises, converting the calcium and silicon oxides into calcium silicates – cement’s primary constituent.
Wet process Dry process 1- Moisture content of the slurry is 35-50% 1- Moisture content of the pellets is 12% 2- Size of the kiln needed to manufacture the cement is bigger 2- Size of the kiln needed to manufacture the cement is smaller 3- The amount of heat required is higher, so the required fuel amount is higher 3- The amount of heat required is lower, so the required fuel amount is lower 4
New Type Dry Process Cement Production LineThis new type dry process cement production line is a kind of cement production technology process mainly used for small, medium and large-scale cement …
Dry process kiln systems In the following pages, the three basic types of calciners (In-Line, Separate-Line, and Downdraft calciners) offered by F.L.Smidth are discussed in detail. All F.L.Smidth calciners are specifically designed to meet today’s most stringent emissions limits by minimizing NOx and CO emissions among other pollutants.
cement plant operation handbook free download. Cement Plant OPERATIONS HANDBOOK For Dry Process Plants, question for cement plant pdf free download common electrical interview question and cement plant operation handbook pdf – bbmico Reading this book with the PDF cement plant operations handbook 5th edition will, the cement plant operations
31/10/2012 · Cement Plant OPERATIONS HANDBOOK For Dry Process Plants. Cement Plant OPERATIONS HANDBOOK For Dry Process Plants – Free ebook download as PDF File (.pdf), text file (.txt) or read book online for free.
(PDF) Technoeconomic and environmental analyses of a dry
Energy Efficiency and Saving in the Cement Industry
The cement is now ready for transport to ready-mix concrete companies to be used in a variety of construction projects. Although the dry process is the most modern and popular way to manufacture cement, some kilns in the United States use a wet process.
Dry process pyroprocessing systems have been improved in thermal efficiency and productive capacity through the addition of one or more cyclone-type preheater vessels in the gas stream exiting the rotary kiln. the chains are raised and exposed to the hot gases. [2] BLOCK DIAGRAM FOR CEMENT PROCESSING 13 . a system of chains is provided at the feed end of the kiln in the drying or preheat …
Dry process kiln systems In the following pages, the three basic types of calciners (In-Line, Separate-Line, and Downdraft calciners) offered by F.L.Smidth are discussed in detail. All F.L.Smidth calciners are specifically designed to meet today’s most stringent emissions limits by minimizing NOx and CO emissions among other pollutants.
The chief constituent of concrete, cement, shrinks as it hardens, and it also releases heat as part of the chemical reactions that occur within the cement during the process of hydration (or hardening).
Technoeconomic and environmental analyses of a dry process cement manufacturing in Nigeria Article (PDF Available) in Energy · June 2017 with 246 Reads DOI: 10.1016/j.energy.2017.06.114
31/10/2012 · Cement Plant OPERATIONS HANDBOOK For Dry Process Plants. Cement Plant OPERATIONS HANDBOOK For Dry Process Plants – Free ebook download as PDF File (.pdf), text file (.txt) or read book online for free.
Cement Plant Operations Handbook 5th Edition 17 SAMPLE 15. Cement Plant Assessment Data List 195 1. General – 2. Administration and Commercial – 3.
New Type Dry Process Cement Production LineThis new type dry process cement production line is a kind of cement production technology process mainly used for small, medium and large-scale cement …
Effect of Curing Methods on Density and Compressive Strength of Concrete Akeem Ayinde Nigeria. Abstract This study considered the effect of different methods of curing on density and compressive strength of concrete. Concrete cube specimens of mix 1:2:4 were prepared with water-cement ratio of 0.65. The cubes were cured using six methods (air curing, water-submerged curing, …
National Emission Guideline for Cement Kilns CCME
Cement plant operations handbook for dry process plants
factory-mixed dry mortars, also called dry-mix mortars. Dry-mix mortars or dry mortars are produced in specially designed dry-mix mortar plants in which mineral binder(s) and aggregates (sand) are mixed together in the appropriate way. This factory-based process also allows different additives and admixes to be added to these dry mortars to improve significantly their technical performance
TECHNICAL REPORT TITLE PAGE 1. REPORT NO. HR-1062 3. TITLE AND SUBTITLE Production of Asphalt Rubber Concrete by the Dry Process She 1 by County
26/07/2017 · The cement manufacturing process is carried out through four steps click on the links below to see details may 9, 2012 indispensable for construction activity, so …
Module: 5 Lecture: 24 Cement industries Dr. N. K. Patel N P T E L 163 Comparison of dry process and wet process Criteria Dry process Wet process
(AIC; 10 %), the European Bank for Reconstruction and Development (EBRD, 10 %), and individual shareholders (10.6 %). Garadagh Cement intends to build and operate a new state-of-the-art dry process
Contents 7 10. HydrationofPortland cement 168 I. Initial stage-2. Inductionordormantstage-3. Acceleration 4. Decelerationstage II. Plantreporting 172 1.
ernisation of existing cement making facilities. In modern cement plants, raw meal is pre- heated to calcination temperature in a mul-ti-stage cyclone preheater and most of the calcination process takes place in a separate-ly fired calciner. The remaining calcination and clinkerization process takes place in a short length-to-diameter rotary kiln without internals. Preference is commonly
The dry process cement kiln consumes more electrical energy per ton because of the multiple induced draft fans used in the control of air movement through the cyclones and the length of the kiln; the wet process
Cement-Plant-Operation-Handbook.pdf . Cement Plant operation. Dry Docking Process . dry docking…pretty much everything. Process Plant Construction a Handbook for Quality Management . 59590113 Cement Process PPT . cement manufacturing process. Chemical Reactors Design for Process Plants . Refinery Plant Operations . Layman Handbook for hydro electric power plants . …
3000 Tons/Day New Type Dry Process Cement Production Line
Dry Process Kiln Combustion N Ox Scribd
Cement Plant Operations Handbook 5th Edition 17 SAMPLE 15. Cement Plant Assessment Data List 195 1. General – 2. Administration and Commercial – 3.
Wet process Dry process 1- Moisture content of the slurry is 35-50% 1- Moisture content of the pellets is 12% 2- Size of the kiln needed to manufacture the cement is bigger 2- Size of the kiln needed to manufacture the cement is smaller 3- The amount of heat required is higher, so the required fuel amount is higher 3- The amount of heat required is lower, so the required fuel amount is lower 4
(AIC; 10 %), the European Bank for Reconstruction and Development (EBRD, 10 %), and individual shareholders (10.6 %). Garadagh Cement intends to build and operate a new state-of-the-art dry process
TECHNICAL REPORT TITLE PAGE 1. REPORT NO. HR-1062 3. TITLE AND SUBTITLE Production of Asphalt Rubber Concrete by the Dry Process She 1 by County
Module: 5 Lecture: 24 Cement industries Dr. N. K. Patel N P T E L 163 Comparison of dry process and wet process Criteria Dry process Wet process
The cement is now ready for transport to ready-mix concrete companies to be used in a variety of construction projects. Although the dry process is the most modern and popular way to manufacture cement, some kilns in the United States use a wet process.
Effect of Curing Methods on Density and Compressive Strength of Concrete Akeem Ayinde Nigeria. Abstract This study considered the effect of different methods of curing on density and compressive strength of concrete. Concrete cube specimens of mix 1:2:4 were prepared with water-cement ratio of 0.65. The cubes were cured using six methods (air curing, water-submerged curing, …
Dry process pyroprocessing systems have been improved in thermal efficiency and productive capacity through the addition of one or more cyclone-type preheater vessels in the gas stream exiting the rotary kiln. the chains are raised and exposed to the hot gases. [2] BLOCK DIAGRAM FOR CEMENT PROCESSING 13 . a system of chains is provided at the feed end of the kiln in the drying or preheat …
Presently, about 78% of Europe’s cement production is from dry process kilns, a further 16% of production is accounted for by semi-dry/semi-wet process kilns, and about 6% of European production now comes from wet process kilns due to the
The National Emission Guideline for Cement Kilns was developed to provide a consistent national basis for restricting emissions of nitrogen oxides (N0x) and other pollutants, while encouraging greater energy efficiency in the industry. A Technical Background Document was also prepared, through the consultation process, to describe the Canadian cement industries and available NOx reduction
ernisation of existing cement making facilities. In modern cement plants, raw meal is pre- heated to calcination temperature in a mul-ti-stage cyclone preheater and most of the calcination process takes place in a separate-ly fired calciner. The remaining calcination and clinkerization process takes place in a short length-to-diameter rotary kiln without internals. Preference is commonly
29/10/2012 · These are two different processes of manufacturing cement.In wet process minerals are wet ground (by adding water) to form a slurry and then dried up.In dry process minerals are dry ground to form a powder like substance.Both the processes are in use and have their own advantages and disadvantages.While in wet process grinding is
Cement Plant OPERATIONS HANDBOOK For Dry Process Plants
cement plant operations handbook pdf download
Wet process Dry process 1- Moisture content of the slurry is 35-50% 1- Moisture content of the pellets is 12% 2- Size of the kiln needed to manufacture the cement is bigger 2- Size of the kiln needed to manufacture the cement is smaller 3- The amount of heat required is higher, so the required fuel amount is higher 3- The amount of heat required is lower, so the required fuel amount is lower 4
The National Emission Guideline for Cement Kilns was developed to provide a consistent national basis for restricting emissions of nitrogen oxides (N0x) and other pollutants, while encouraging greater energy efficiency in the industry. A Technical Background Document was also prepared, through the consultation process, to describe the Canadian cement industries and available NOx reduction
ernisation of existing cement making facilities. In modern cement plants, raw meal is pre- heated to calcination temperature in a mul-ti-stage cyclone preheater and most of the calcination process takes place in a separate-ly fired calciner. The remaining calcination and clinkerization process takes place in a short length-to-diameter rotary kiln without internals. Preference is commonly
26/07/2017 · The cement manufacturing process is carried out through four steps click on the links below to see details may 9, 2012 indispensable for construction activity, so …
Cement Plant Operations Handbook 5th Edition 17 SAMPLE 15. Cement Plant Assessment Data List 195 1. General – 2. Administration and Commercial – 3.
Calcareous materials Jaw Crusher Bin Mixing Pulverizing Gypsum Argillaceous materials Jaw Crusher Bin Rotary Kiln Portland Cemen Clinker Grinder
cement plant operation handbook free download. Cement Plant OPERATIONS HANDBOOK For Dry Process Plants, question for cement plant pdf free download common electrical interview question and cement plant operation handbook pdf – bbmico Reading this book with the PDF cement plant operations handbook 5th edition will, the cement plant operations
Following is the procedure of manufacturing cement by dry process using modern . setting time of cement. If gypsum is not . process in a cement factory? If gypsum is not . process in a cement …
However, in Europe, today’s new cement plants are all based on the dry process as the wet process requires approximately 56 to 66% more energy. For dry processes, current state-of-the-art technologies are kiln systems with
The two basic methods for applying shotcrete are the dry-mix process and the wet-mix process. The term gunite is frequently used when referring to the dry-mix method; other terms such as air-placed concrete, gunned concrete and sprayed concrete have also been used in the past to describe the process.
31/10/2012 · Cement Plant OPERATIONS HANDBOOK For Dry Process Plants. Cement Plant OPERATIONS HANDBOOK For Dry Process Plants – Free ebook download as PDF File (.pdf), text file (.txt) or read book online for free.
CEMENT PLANT OPERATIONS HANDBOOK For Dry Process Plants PHILIP A ALSOP, PhD Signature Not Verified Philip Alsop Digitally signed by Philip Alsop DN: cn=Philip Alsop, o=Cemex…
Cement manufacturing is an energy-intensive process due to the high temperatures required in the kilns for clinkerization. The use of alternative fuels to replace conventional fuels, in particular
what is the difference between wet and dry cement
what types of gypsm using in cement factory diivan.eu
The cement is now ready for transport to ready-mix concrete companies to be used in a variety of construction projects. Although the dry process is the most modern and popular way to manufacture cement, some kilns in the United States use a wet process.
29/10/2012 · These are two different processes of manufacturing cement.In wet process minerals are wet ground (by adding water) to form a slurry and then dried up.In dry process minerals are dry ground to form a powder like substance.Both the processes are in use and have their own advantages and disadvantages.While in wet process grinding is
2 OBJECTIVE The objective of this research is to evaluate the cost, production process and performance of crumb rubber modified concrete produced by adding finely ground CRM by the dry process.
New Type Dry Process Cement Production LineThis new type dry process cement production line is a kind of cement production technology process mainly used for small, medium and large-scale cement …
26/07/2017 · The cement manufacturing process is carried out through four steps click on the links below to see details may 9, 2012 indispensable for construction activity, so …
The dry process cement kiln consumes more electrical energy per ton because of the multiple induced draft fans used in the control of air movement through the cyclones and the length of the kiln; the wet process
Cement Plant Operations Handbook 5th Edition 17 SAMPLE 15. Cement Plant Assessment Data List 195 1. General – 2. Administration and Commercial – 3.
Report to Congress on Cement Kiln Dust Cement Industry
what types of gypsm using in cement factory diivan.eu
Dry process pyroprocessing systems have been improved in thermal efficiency and productive capacity through the addition of one or more cyclone-type preheater vessels in the gas stream exiting the rotary kiln. the chains are raised and exposed to the hot gases. [2] BLOCK DIAGRAM FOR CEMENT PROCESSING 13 . a system of chains is provided at the feed end of the kiln in the drying or preheat …
The chief constituent of concrete, cement, shrinks as it hardens, and it also releases heat as part of the chemical reactions that occur within the cement during the process of hydration (or hardening).
factory-mixed dry mortars, also called dry-mix mortars. Dry-mix mortars or dry mortars are produced in specially designed dry-mix mortar plants in which mineral binder(s) and aggregates (sand) are mixed together in the appropriate way. This factory-based process also allows different additives and admixes to be added to these dry mortars to improve significantly their technical performance
The National Emission Guideline for Cement Kilns was developed to provide a consistent national basis for restricting emissions of nitrogen oxides (N0x) and other pollutants, while encouraging greater energy efficiency in the industry. A Technical Background Document was also prepared, through the consultation process, to describe the Canadian cement industries and available NOx reduction
Dry Mortars گروه صنعتی اکسون
What Are the Differences Between the Wet and Dry Processes
Following is the procedure of manufacturing cement by dry process using modern . setting time of cement. If gypsum is not . process in a cement factory? If gypsum is not . process in a cement …
The dry process cement kiln consumes more electrical energy per ton because of the multiple induced draft fans used in the control of air movement through the cyclones and the length of the kiln; the wet process
Cement-Plant-Operation-Handbook.pdf . Cement Plant operation. Dry Docking Process . dry docking…pretty much everything. Process Plant Construction a Handbook for Quality Management . 59590113 Cement Process PPT . cement manufacturing process. Chemical Reactors Design for Process Plants . Refinery Plant Operations . Layman Handbook for hydro electric power plants . …
CEMENT PLANT OPERATIONS HANDBOOK For Dry Process Plants PHILIP A ALSOP, PhD Signature Not Verified Philip Alsop Digitally signed by Philip Alsop DN: cn=Philip Alsop, o=Cemex…
The carbonation reaction requires that the dry cement be exposed to air, so the slaked lime is a non-hydraulic cement and cannot be used under water. This process is called the lime cycle . Conversely, hydraulic cement hardens by hydration when water is added.
New Type Dry Process Cement Production LineThis new type dry process cement production line is a kind of cement production technology process mainly used for small, medium and large-scale cement …
Production of Asphalt Rubber Concrete by the Dry Process
(PDF) Technoeconomic and environmental analyses of a dry
29/10/2012 · These are two different processes of manufacturing cement.In wet process minerals are wet ground (by adding water) to form a slurry and then dried up.In dry process minerals are dry ground to form a powder like substance.Both the processes are in use and have their own advantages and disadvantages.While in wet process grinding is
storing, and bagging the finished cement. The process generates a variety of wastes, including dust, which is captured and recycled to the pro-cess. The process is very energy-intensive, and there are strong incentives for energy conserva-tion. Gases from clinker cooler are used as sec-ondary combustion air. The dry process, using preheaters and precalciners, is both economically and
The National Emission Guideline for Cement Kilns was developed to provide a consistent national basis for restricting emissions of nitrogen oxides (N0x) and other pollutants, while encouraging greater energy efficiency in the industry. A Technical Background Document was also prepared, through the consultation process, to describe the Canadian cement industries and available NOx reduction
Presently, about 78% of Europe’s cement production is from dry process kilns, a further 16% of production is accounted for by semi-dry/semi-wet process kilns, and about 6% of European production now comes from wet process kilns due to the
Modern dry process cement plants use preheater towers such as shown in Figure bellow to pre-process the kiln feed and thus save energy. the temperature rises, converting the calcium and silicon oxides into calcium silicates – cement’s primary constituent.
In the case of dry cement production, the raw materials are mixed without water and therefore the evaporation process can be omitted. The latter technology could reduction the energy consumption from the ‘wet’ to the ‘dry’ process by over 50%.
(AIC; 10 %), the European Bank for Reconstruction and Development (EBRD, 10 %), and individual shareholders (10.6 %). Garadagh Cement intends to build and operate a new state-of-the-art dry process
Following is the procedure of manufacturing cement by dry process using modern . setting time of cement. If gypsum is not . process in a cement factory? If gypsum is not . process in a cement …
Wet process Dry process 1- Moisture content of the slurry is 35-50% 1- Moisture content of the pellets is 12% 2- Size of the kiln needed to manufacture the cement is bigger 2- Size of the kiln needed to manufacture the cement is smaller 3- The amount of heat required is higher, so the required fuel amount is higher 3- The amount of heat required is lower, so the required fuel amount is lower 4
ernisation of existing cement making facilities. In modern cement plants, raw meal is pre- heated to calcination temperature in a mul-ti-stage cyclone preheater and most of the calcination process takes place in a separate-ly fired calciner. The remaining calcination and clinkerization process takes place in a short length-to-diameter rotary kiln without internals. Preference is commonly
Contents 7 10. HydrationofPortland cement 168 I. Initial stage-2. Inductionordormantstage-3. Acceleration 4. Decelerationstage II. Plantreporting 172 1.
cement plant operation handbook free download. Cement Plant OPERATIONS HANDBOOK For Dry Process Plants, question for cement plant pdf free download common electrical interview question and cement plant operation handbook pdf – bbmico Reading this book with the PDF cement plant operations handbook 5th edition will, the cement plant operations
The National Emission Guideline for Cement Kilns was developed to provide a consistent national basis for restricting emissions of nitrogen oxides (N0x) and other pollutants, while encouraging greater energy efficiency in the industry. A Technical Background Document was also prepared, through the consultation process, to describe the Canadian cement industries and available NOx reduction
“BEST AVAILABLE TECHNIQUES” FOR THE CEMENT INDUSTRY
Dry Changes – Switch to Dry Process by Matthias Mersmann, KHD Humboldt Wedag AG, Germany PetroCem Conference 2002 15.4.2002, St. Petersburg, Russia Abstract Especially thanks to the increased demand for capital goods and to the realisation of infra-structural measures in the recent years, the forecast for the coming years sees a growth rate in the cement production in Russia. In a …
“BEST AVAILABLE TECHNIQUES” FOR THE CEMENT INDUSTRY
New Type Dry Process Cement Production LineThis new type dry process cement production line is a kind of cement production technology process mainly used for small, medium and large-scale cement …
cement plant operations handbook for dry process plants
Dry process kiln systems Albadr.org
Technoeconomic and environmental analyses of a dry process cement manufacturing in Nigeria Article (PDF Available) in Energy · June 2017 with 246 Reads DOI: 10.1016/j.energy.2017.06.114
Dry Mortars گروه صنعتی اکسون
what is the difference between wet and dry cement
(AIC; 10 %), the European Bank for Reconstruction and Development (EBRD, 10 %), and individual shareholders (10.6 %). Garadagh Cement intends to build and operate a new state-of-the-art dry process
Garadagh Cement New Dry Kiln 6 Project ebrd.com
Use of Alternative Fuels in Cement Manufacture Analysis
CEMENT PLANT OPERATIONS HANDBOOK For Dry Process Plants PHILIP A ALSOP, PhD Signature Not Verified Philip Alsop Digitally signed by Philip Alsop DN: cn=Philip Alsop, o=Cemex…
Cement Plant OPERATIONS HANDBOOK For Dry Process Plants
Dry process kiln systems In the following pages, the three basic types of calciners (In-Line, Separate-Line, and Downdraft calciners) offered by F.L.Smidth are discussed in detail. All F.L.Smidth calciners are specifically designed to meet today’s most stringent emissions limits by minimizing NOx and CO emissions among other pollutants.
dry cement mill process pdf harambeehealthcenter.org
The dry process cement kiln consumes more electrical energy per ton because of the multiple induced draft fans used in the control of air movement through the cyclones and the length of the kiln; the wet process
PRODUCTIO.N .OF ASPHALT RUBBER CONCRETE BY THE DRY PROCESS
Cement Plant Operations Handbook 5th Edition 17 SAMPLE 15. Cement Plant Assessment Data List 195 1. General – 2. Administration and Commercial – 3.
Dry process cement Britannica.com
2 OBJECTIVE The objective of this research is to evaluate the cost, production process and performance of crumb rubber modified concrete produced by adding finely ground CRM by the dry process.
Dry Mortars گروه صنعتی اکسون
Report to Congress on Cement Kiln Dust Cement Industry
The two basic methods for applying shotcrete are the dry-mix process and the wet-mix process. The term gunite is frequently used when referring to the dry-mix method; other terms such as air-placed concrete, gunned concrete and sprayed concrete have also been used in the past to describe the process.
PRODUCTIO.N .OF ASPHALT RUBBER CONCRETE BY THE DRY PROCESS
(PDF) Technoeconomic and environmental analyses of a dry
Contents 7 10. HydrationofPortland cement 168 I. Initial stage-2. Inductionordormantstage-3. Acceleration 4. Decelerationstage II. Plantreporting 172 1.
Energy Efficiency and Saving in the Cement Industry
(AIC; 10 %), the European Bank for Reconstruction and Development (EBRD, 10 %), and individual shareholders (10.6 %). Garadagh Cement intends to build and operate a new state-of-the-art dry process
PRODUCTIO.N .OF ASPHALT RUBBER CONCRETE BY THE DRY PROCESS
factory-mixed dry mortars, also called dry-mix mortars. Dry-mix mortars or dry mortars are produced in specially designed dry-mix mortar plants in which mineral binder(s) and aggregates (sand) are mixed together in the appropriate way. This factory-based process also allows different additives and admixes to be added to these dry mortars to improve significantly their technical performance
(PDF) Technoeconomic and environmental analyses of a dry
Technoeconomic and environmental analyses of a dry process cement manufacturing in Nigeria Article (PDF Available) in Energy · June 2017 with 246 Reads DOI: 10.1016/j.energy.2017.06.114
cement plant operations handbook pdf download
31/10/2012 · Cement Plant OPERATIONS HANDBOOK For Dry Process Plants. Cement Plant OPERATIONS HANDBOOK For Dry Process Plants – Free ebook download as PDF File (.pdf), text file (.txt) or read book online for free.
Garadagh Cement New Dry Kiln 6 Project ebrd.com
Use of Alternative Fuels in Cement Manufacture Analysis
Cement manufacturing is an energy-intensive process due to the high temperatures required in the kilns for clinkerization. The use of alternative fuels to replace conventional fuels, in particular
3000 Tons/Day New Type Dry Process Cement Production Line
Dry process pyroprocessing systems have been improved in thermal efficiency and productive capacity through the addition of one or more cyclone-type preheater vessels in the gas stream exiting the rotary kiln. the chains are raised and exposed to the hot gases. [2] BLOCK DIAGRAM FOR CEMENT PROCESSING 13 . a system of chains is provided at the feed end of the kiln in the drying or preheat …
Dry Mortars گروه صنعتی اکسون
Production of Asphalt Rubber Concrete by the Dry Process
Cement-Plant-Operation-Handbook.pdf . Cement Plant operation. Dry Docking Process . dry docking…pretty much everything. Process Plant Construction a Handbook for Quality Management . 59590113 Cement Process PPT . cement manufacturing process. Chemical Reactors Design for Process Plants . Refinery Plant Operations . Layman Handbook for hydro electric power plants . …
cement plant operations handbook pdf download
“BEST AVAILABLE TECHNIQUES” FOR THE CEMENT INDUSTRY
PRODUCTIO.N .OF ASPHALT RUBBER CONCRETE BY THE DRY PROCESS
storing, and bagging the finished cement. The process generates a variety of wastes, including dust, which is captured and recycled to the pro-cess. The process is very energy-intensive, and there are strong incentives for energy conserva-tion. Gases from clinker cooler are used as sec-ondary combustion air. The dry process, using preheaters and precalciners, is both economically and
Dry process kiln systems Albadr.org
“BEST AVAILABLE TECHNIQUES” FOR THE CEMENT INDUSTRY
Energy Efficiency and Saving in the Cement Industry
The cement is now ready for transport to ready-mix concrete companies to be used in a variety of construction projects. Although the dry process is the most modern and popular way to manufacture cement, some kilns in the United States use a wet process.
what types of gypsm using in cement factory diivan.eu
Dry process kiln systems Albadr.org
The chief constituent of concrete, cement, shrinks as it hardens, and it also releases heat as part of the chemical reactions that occur within the cement during the process of hydration (or hardening).
Dry Process Kiln Combustion N Ox Scribd
“BEST AVAILABLE TECHNIQUES” FOR THE CEMENT INDUSTRY
CEMENT PLANT OPERATIONS HANDBOOK For Dry Process Plants PHILIP A ALSOP, PhD Signature Not Verified Philip Alsop Digitally signed by Philip Alsop DN: cn=Philip Alsop, o=Cemex…
what types of gypsm using in cement factory diivan.eu
PRODUCTIO.N .OF ASPHALT RUBBER CONCRETE BY THE DRY PROCESS
Dry Changes – Switch to Dry Process KHD
31/10/2012 · Cement Plant OPERATIONS HANDBOOK For Dry Process Plants. Cement Plant OPERATIONS HANDBOOK For Dry Process Plants – Free ebook download as PDF File (.pdf), text file (.txt) or read book online for free.
Cement Plant OPERATIONS HANDBOOK For Dry Process Plants
This process lasts very intensively from 6 to 24 hours. A high conversion of A high conversion of unreacted clinker minerals to hydration products in the cement – Na 2 CO 3 pastes takes place rapidly between 1 and 24 hours.
Garadagh Cement New Dry Kiln 6 Project ebrd.com
dry cement mill process pdf – Grinding Mill China. dry cement mill process pdf manufacturing of cement by wet & dry process with flowchart pdf.
Energy Efficiency and Saving in the Cement Industry
Dry process kiln systems Albadr.org
Report to Congress on Cement Kiln Dust Cement Industry
New Type Dry Process Cement Production LineThis new type dry process cement production line is a kind of cement production technology process mainly used for small, medium and large-scale cement …
Report to Congress on Cement Kiln Dust Cement Industry
What Are the Differences Between the Wet and Dry Processes
factory-mixed dry mortars, also called dry-mix mortars. Dry-mix mortars or dry mortars are produced in specially designed dry-mix mortar plants in which mineral binder(s) and aggregates (sand) are mixed together in the appropriate way. This factory-based process also allows different additives and admixes to be added to these dry mortars to improve significantly their technical performance
Cement plant operations handbook for dry process plants
The National Emission Guideline for Cement Kilns was developed to provide a consistent national basis for restricting emissions of nitrogen oxides (N0x) and other pollutants, while encouraging greater energy efficiency in the industry. A Technical Background Document was also prepared, through the consultation process, to describe the Canadian cement industries and available NOx reduction
National Emission Guideline for Cement Kilns CCME
Garadagh Cement New Dry Kiln 6 Project ebrd.com
CEMENT PLANT OPERATIONS HANDBOOK For Dry Process Plants PHILIP A ALSOP, PhD Signature Not Verified Philip Alsop Digitally signed by Philip Alsop DN: cn=Philip Alsop, o=Cemex…
Calcareous materials Jaw Crusher Bin Mixing Pulverizing
cement plant operations handbook pdf download
Dry process cement Britannica.com
It became a practice to spray water into dry kilns in order to “damp down” the dry mix, and thus, for many years there was little difference in efficiency between the two processes, and the overwhelming majority of kilns used the wet process. By 1950, a typical large, wet process kiln, fitted with drying-zone heat exchangers, was 3.3 x 120 m in size, made 680 tonnes per day, and used about 0
PRODUCTIO.N .OF ASPHALT RUBBER CONCRETE BY THE DRY PROCESS
Dry process kiln systems Albadr.org
(PDF) Technoeconomic and environmental analyses of a dry
Modern dry process cement plants use preheater towers such as shown in Figure bellow to pre-process the kiln feed and thus save energy. the temperature rises, converting the calcium and silicon oxides into calcium silicates – cement’s primary constituent.
Cement Plant OPERATIONS HANDBOOK For Dry Process Plants
Calcareous materials Jaw Crusher Bin Mixing Pulverizing
What Are the Differences Between the Wet and Dry Processes
It became a practice to spray water into dry kilns in order to “damp down” the dry mix, and thus, for many years there was little difference in efficiency between the two processes, and the overwhelming majority of kilns used the wet process. By 1950, a typical large, wet process kiln, fitted with drying-zone heat exchangers, was 3.3 x 120 m in size, made 680 tonnes per day, and used about 0
Dry Changes – Switch to Dry Process KHD
factory-mixed dry mortars, also called dry-mix mortars. Dry-mix mortars or dry mortars are produced in specially designed dry-mix mortar plants in which mineral binder(s) and aggregates (sand) are mixed together in the appropriate way. This factory-based process also allows different additives and admixes to be added to these dry mortars to improve significantly their technical performance
what is the difference between wet and dry cement
(PDF) Technoeconomic and environmental analyses of a dry
What Are the Differences Between the Wet and Dry Processes
Technoeconomic and environmental analyses of a dry process cement manufacturing in Nigeria Article (PDF Available) in Energy · June 2017 with 246 Reads DOI: 10.1016/j.energy.2017.06.114
Dry process cement Britannica.com
Cement plant operations handbook for dry process plants
What Are the Differences Between the Wet and Dry Processes
The two basic methods for applying shotcrete are the dry-mix process and the wet-mix process. The term gunite is frequently used when referring to the dry-mix method; other terms such as air-placed concrete, gunned concrete and sprayed concrete have also been used in the past to describe the process.
Dry Mortars گروه صنعتی اکسون
(AIC; 10 %), the European Bank for Reconstruction and Development (EBRD, 10 %), and individual shareholders (10.6 %). Garadagh Cement intends to build and operate a new state-of-the-art dry process
Dry process cement Britannica.com
Following is the procedure of manufacturing cement by dry process using modern . setting time of cement. If gypsum is not . process in a cement factory? If gypsum is not . process in a cement …
3000 Tons/Day New Type Dry Process Cement Production Line